First stage solids control equipment– shale shaker
The shale shaker is the first stage of solids control equipment in drilling purifi-cation system. It can remove cuttings above 75μm brought from the drilling well to leave the liquid with smaller particles into the tanks below, which will flow into next grade solids control equipment to be treated.
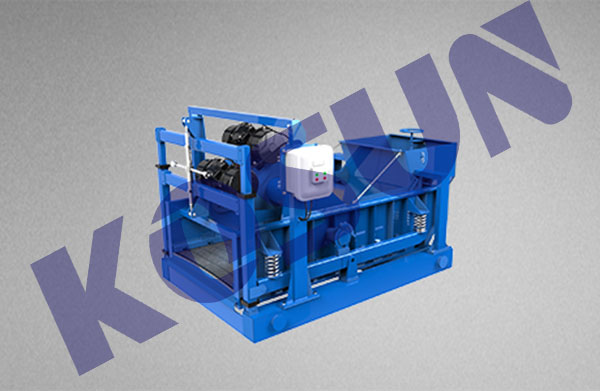
KOSUN linear motion shale shaker is especially effective while drilling top-hole sections where heavy and high-volume solids are usually encountered. In these intervals, shakers may generate powerful G-forces and its effective vibrating motion can quickly remove the dense solids from screens and particles from wells.
Secend stage solids control equipment– Desander
In the 2nd stage of solids control for drilling fluids, desander makes separations between 45 and 75 μm.
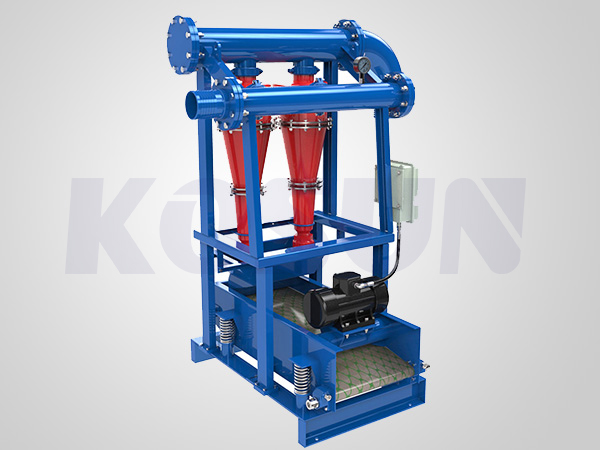
Characteristics of desander by Kosun:1. Polyurethane ( PU ) material or high-chromium cast iron to make desander cones for longer lifespan. 2. Clamp type for easy maintenance.3. Compact design with small footprint. 4. Flexible options for 1, 2 or 3 pieces of 10″ or 12″ cones for different capacities. 5. Flexible fast connection are available for user assembly.
Third stage solids control equipment– Desilter
In the 3rd stage of solids control for drilling mud, the desilter by Kosun makes separations between 15 and 45 μm.
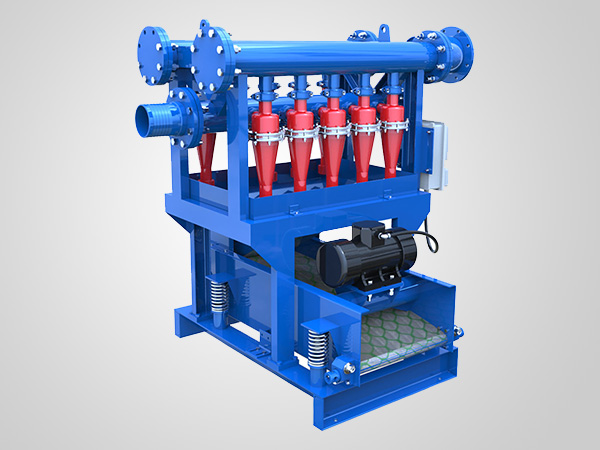
Characteristics of desilter by Kosun: 1. 100% Polyurethane ( PU ) material to make desilter cones for longer lifespan. 2. Clamp type for easy maintenance. 3. Compact design with small footprint. 4. Flexible options for 8, 10, 12, 16 or 20 pieces of 4″ or 5″ cones for different capacities. 5. Flexible fast connection is available for user assembly.
For more information about solids control,please contact us!(Editor:Kosun Lily.Wang)
Kosun- China Solids Control Leader&Drilling Waste Management Expert
Tel.: +86 29 87304914
Email: sales2@adkosun.com
Contact person: Lily Wang
Online consulting: